Hazard Identification and Risk Assessment (HIRA): What is it and how can it be used?
- ORS
- Jul 2, 2024
- 6 min read
Updated: Feb 20
In this article:
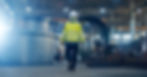
Definition and Intention of HIRA
Hazard Identification and Risk Assessment (HIRA) in the industrial risk management is a systematic methodology which directs focus towards hazards that potentially could lead to fatalities, injuries and other damage. The emphasise of the analysis is identification and evaluation of relevant risks, so that appropriate control measures can be implemented to establish a safer work environment and protect employees from harm.
The overall objective of HIRA is to reduce the likelihood and severity of major accidents, injuries, and environmental damage.
Overview and Methodology for HIRA
HIRA consists of hazard identification and risk assessment respectively. The initial focus is to identify potential hazards within a process, while the secondary step is to assess the process-related risks according to certain evaluation factors.
Data collection with Hazard Identification
Hazard identification constitutes the basic condition for a successful HIRA according to safety measurements. In this part, direct focus is on physical inspections of equipment and handling procedures within the workspace areas and processes. This, in order to identify potential risks with regards to human health and safety.
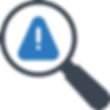
It is imperative for organizations to understand and identify all risks that employees and the organization might face throughout operations. The risks can vary significantly in terms of sort and appearance. Therefore, it is relevant to identify anything that might seem to be deviating or having an unusual behaviour. In practical terms, this allows for the identification of various hazards, including physical, mechanical, electrical, fire and explosion, thermal, radiological, acoustic, and vibrational.
Risk Assessment

As a follow-up on the hazard identification, a risk assessment is made with regards to specific risk criteria. In this stage, the assessment starts by determining how the hazardous events generate certain impacts. Not uncommonly, these impacts are related to human safety, environmental disturbance and/or asset damage/loss of production. In some cases, also reputational impact can be part of the assessment if founded necessary.
The risk assessment is the process where identified hazardous risks are evaluated in terms of their severity, likelihood, and other factors. From here, assessing risks becomes a process of deciding if these are low or high risk hazards. The execution of this risk assessment can be done in three ways: qualitative, quantitative, and semi-quantitative. Not uncommonly, one type of risk assessment is complemented with another assessment to increase the accuracy rate.
The result of the risk assessment usually consists of a list with all identified hazards where most have been risk ranked according to risk criteria. The risk rating can either be low, medium or high. A low risk usually means that the risk is acceptable and no risk reduction is necessary. A medium risk usually means that there is a need for a handling procedure to reduce the risk. This risk reduction should follow the ALARP (As Low As Reasonably Practicable) principle, which means that the risk should be reduced to an extent that is assumed as reasonable with regards to effort, money and time. A high risk represents a scenario that is non-acceptable. If there is a red scenario, immediate action is required to manage the hazard. To reduce the risk, actions can be stated for the responsible party to follow-up and manage. The responsible party must also prove the completion of the action follow-up in writing.

HIRA vs HAZOP - What are the differences?
The are many similarities between HIRA and HAZOP (Hazard and Operability Study). Generally, the methods are close to each other and can often be utilized in a larger risk management perspective. However, HIRA can be considered more comprehensive, with more focus towards identification of hazards. Contrary, HAZOP can be considered as more detailed in terms of assessing the risks. Observed deviations and potential for hazardous events are more focused on particular equipment and material within a system.
If you are more interested in detailed risk assessments, please read our other articles covering HAZOP methodology.
Classification and Categorization of HIRA
Faults within process, equipment or/and human factor - Most common risk factors
Prior to the risk assessment, the identified hazards are categorized and divided into groups with regards to their characteristics. Normally, identified hazards are either related to process, equipment or human factor. Depending on the characteristics of a hazard, the risk assessment is made accordingly to efficiently target the issues. This way, it is easier to add adequate control measures.
Implementing HIRA Study
Implementing HIRA in industrial practice means active changes on high level as on low level. On high level it is usually a matter of management control and attitude to the concept. On the other hand, low level management refers to tangible contribution of specific controls, e.g. adaptations of individual departments within the industry.

High level
Basically, HIRA involves building and implementing a safety strategy based on the prior identification, assessment, and analyses. For this to happen, it must be stated among the decision-making authorities that it is what the organization strives for and intends to further comply with. A successful implementation therefore requires influential disciplines that are able to argue and convince people in higher management positions that HIRA is relevant and important for business.
Low level
As soon as HIRA has been determined to be executed, this means that relevant departments and sub-departments need to be informed. For a successful implementation of HIRA and accurate placing of control measures, this means inclusion of engineering, administrative and operational staff. Together, these people should be able to state organize what action and control measures that need to be implemented. For example, this means evaluation of need for personal protective equipment, Permit To Work (PTW), new guidelines and rules for operations etc.
Continuous monitoring, evaluation and reviews

For a resilient and developing HIRA implementation, it is of great relevance to evaluate previous actions and adaptations in the business. Preferably, this is performed by monitoring and reviewing the effectiveness of controls and safety measures.
Step-by-step Guide to HIRA - A strategy that works

The challenging part of implementing a new safety format into a business is often that people get overwhelmed feeling due to the load of information. Therefore, it is handy to have a comprehensive guide to HIRA that sufficiently and concretely breaks down possible obstacles on the way. A handbook with guiding steps is usually necessary for building a foundation for future policies.
In this handbook, it should be clearly stated, like a checklist, what the organization should conduct for an adequate and successful HIRA. Concretely, on general level, this means regular inspections, hazard analysis, and incident investigations to identify hazards. In addition, separate actions might be implemented suggested by the actual organization or company. Moreover, documentation of possible changes in design, operations etc. is crucial for future transparency.
Simply, a step-by-step guide to HIRA involves identifying hazards, evaluating risks, building and implementing a safety strategy, monitoring and reviewing, and creating a checklist.
Conclusion
Effective HIRA for risk assessments
As previously stated, an effective HIRA is crucial for maintaining a high level of safety and efficiency in a workplace. In some cases, implementation of HIRA with target-oriented control measures can make a life-saving difference.
The methodology for a HIRA circulates around two principles: 1) Hazard identification and 2) Risk assessment.
The first part involves identifying hazards with regards to process risks, equipment risks and/or risks related to the influence of the human factor. In this phase, potential risks are spotted through physical inspections and/or deviations in documentation, e.g., deficiencies in handling procedures or similar.
The second part involves assessing risks from the hazard identification part. In this phase, the identified hazards are assessed with regards to various impacts, such as human safety, environmental disturbance and/or asset damage/loss of production. The hazardous events are further analysed by ranking the risk. If needed, actions are stated for responsible part to manage and later prove in writing for completion and action close-out.
By following a comprehensive hazard identification and risk assessment process, organizations can reduce the risk of accidents, injuries, and environmental damage. The simplest way to execute this is by following a step-by-step method, often presented as a checklist.
Our recommendation
Identifying and assessing workplace hazards can be challenging when an organization's risk analysis procedures lack appropriate methods. Usually, the issue lies in the uncertainty on how it shall be executed in suitable way. HIRA may be the answer to this problem thanks to its simplicity and straight-forwardness. If you want to know more about HIRA, or any of our other services, do not hesitate to contact us.