Failure Mode, Effects and Criticality Analysis (FMECA)
- Manar Rekabi | Senior Consultant
- Mar 27, 2024
- 6 min read
Updated: Mar 14
In this article:
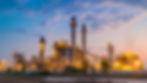
Failure Modes and Effects Analysis (FMEA) is a systematic technique used to analyze potential failures in technical systems. Originating in the late 1940s. Generally, FMEA is utilized to identify and describe possible failure modes, failure causes, and failure effects. When describing or ranking the severity of various failures is added, the technique is called Failure Modes, Effects and Criticality Analysis (FMECA).
FMECA is primarily employed during the design phase of a technical system to identify and analyze potential failures. The analysis is qualitative but may also incorporate some quantitative elements such as specifying the failure rate of each failure mode and ranking the severity of the failure effects.
FMECA can also be used in later phases of a system’s life cycle. The objective at that point is to identify parts of the system that require enhancement to meet specific safety or reliability requirements or to provide input for maintenance planning.
Purpose and Objective of FMECA
The objective of FMECA is to review as many components, assemblies, and subsystems as possible with the goal of identifying, evaluating, and prioritizing potential failure modes of the system, along with their associated effects and criticality. This aims to implement appropriate hazards mitigation strategies and improve reliability, safety, and performance.
The main purposes of FMECA can be summarized as follows:
Identifying failure modes affecting system operation or user safety.
Describing how each failure mode can be detected.
Determining the criticality of each failure mode.
Providing a comprehensive overview of system weaknesses for cost-effective improvements.
Offering guidelines for the development and support of inspection, testing, and maintenance programs aims to prevent failure, thereby reducing corrective maintenance and downtime.
FMECA Process
The FMECA analysis is executed by systemically reviewing selected subsystem, functions, and components to identify failure modes, causes, and effects of such failures. For each component, the failure modes and their resulting effects on the rest of the system, safeguards and criticality are recorded in the FMECA worksheet.

The FMECA is carried out in several steps, which include:
1- System Breakdown
The system is broken down into subsystems based on interrelationships among its various subsystems. The number of levels used in the breakdown depends on the objective of the FMECA study. Subsequently, the components of each subsystem are identified.

2-Â Define the Operational Mode and Function of each Component
For each component, the operational mode, describing the specific state or condition in which the component operates, and the function, referring to the specific role or task the component performs within the system, are defined.
3-Â Identify Failure Modes, Causes, and Detection Methods (Controls)
For each component, relevant failure modes, indicating how a component could fail to meet its intended function or purpose, as well as the causes of failures, underlying reasons or mechanisms leading to a failure mode, are identified. Additionally, the methods of failure detection (controls), which encompass possible ways to detect, prevent and mitigate the consequences and frequency of each identified failure mode, are recorded.
4-Â Determine Failure Modes Consequences
For each failure mode, credible consequences are determined and recorded. These consequences are divided into parts: local consequences, representing the impact of the failure mode on the next higher level in the hierarchy, and global consequences, representing the impact of failure mode on the entire system.
5- Assign Criticality Level (Risk) for each Failure Mode
To prioritize possible failure modes, a risk priority number is assigned to each failure mode, indicating the degree of importance. Typically, this number is determined through criticality analysis by using a Criticality Matrix (Risk Matrix), which comprises two axes: Severity and Likelihood of Occurrence. On the severity axis, the potential impact or consequences of each failure mode are assessed, often categorized into levels such as minor, moderate, major, and critical, based on specific analysis needs. The likelihood of occurrence axis evaluates the probability or frequency of each failure mode occurring, typically categorized into levels such as unlikely, possible, occasional, and frequent.
An example of the Criticality Matrix is shown in Figure 3, and an example of the FMECA worksheet is shown in figure 4


Resources and Skills Required for FMECA Analysis
Conducting an FMECA study effectively and accurately necessitates a diverse team comprising individuals from various disciplines who possess a deep understanding of FMECA methodologies and techniques. Typically, the FMECA team may include the following experts, among others:
Facilitator (Engineer): Possesses extensive knowledge in reliability, safety and risk assessment. His primary role is to guide the FMECA team through the analysis process, foster participation, facilitate discussions, and ensure the fulfillment of objectives.
Design Engineers (during design process): Play a pivotal role in FMECA studies, particularly during the initial stages of system development, leveraging his comprehensive understanding of system architecture, components, and functionality.
System Engineers: Essential for conducting robust FMECA studies, given their comprehensive grasp of the entire system, encompassing subsystems, interfaces, and operational requirements.Â
Process Engineers: Integral to FMECA studies, contributing significantly to evaluating how possible failure modes could impact overall process efficiency, productivity, and quality, thereby helping criticality analysis.
Maintenance Engineers: Provide crucial technical expertise in FMECA studies, offering valuable insights into the root causes of possible failure modes and recommending optimal maintenance activities for the system, including preventive, corrective, and predictive maintenance.
The composition and size of the FMECA team, as well as the number of experts participating in the workshop, primarily depend on the nature of the system under study in terms of maturity and complexity, as well as the focus of the study. Moreover, the team should possess a thorough understanding of the study object, its application, and the operating conditions of the system.
Advantages and Limitations of Using FMECA
Building on the preceding description, the advantages and limitations of FMECA can be succinctly identified and clarified as follows.
The advantages of FMECA are:
It facilitates the identification and prioritization of failure according to their potential impact on system performance or safety, enabling organizations to allocate resources effectively by addressing the most critical issues foremost.
It helps in identifying possible failure modes early in the design or operational phase, empowering organizations to implement preventive maintenance strategies to mitigate the risks associated with these failures. This can lead to increased reliability and reduced downtime.
It identifies weaknesses in the system during the design phase, facilitating enhancements that improve reliability and performance before system deployment.
FMECA provides valuable information for decision-making processes related to risk management, resource allocation, and system design. It helps organizations make informed decisions about where to invest resources to minimize risks effectively.
FMECA is highly significant in safety-critical industries like aerospace, automotive, and healthcare. It enables organizations to demonstrate compliance with regulatory requirements by systematically assessing and mitigating risks.
The limitations of FMECA are:
It is heavily dependent on the expertise and judgment of the individuals conducting the analysis. Varying analysts may prioritize each failure mode differently during criticality analysis, resulting in inconsistent outcomes.
It can become complex, particularly for large and interconnected systems when the number of potential failure modes is extensive. Handling and analyzing the substantial volume of data produced by FMECA can pose challenges and be time-consuming.
It demands significant time, effort, and resources when conducted comprehensively. Organizations should deploy dedicated personnel to effectively carry out the analysis.
It aims to identify potential failure modes based on historical data and expert knowledge. However, it may not accurately predict future failures, especially for complex systems with unforeseen interactions or environmental factors.
It is typically performed as a one-time analysis at a specific point in time. It may not account for changes in the system over its lifecycle or new failures that may arise due to evolving technologies or operating conditions.
FMECA and Reliability Centered Maintenance (RCM)
FMECA and RCM are complementary methodologies that synergize to bolster system reliability and maintainability. FMECA sets the foundation by identifying critical failure and their impacts, while RCM translates these insights into practical maintenance strategies aimed at optimizing system performance and mitigating risks.
The relationship between FMECA and RCM is evident as FMECA typically serves as the initial phase in the RCM process. Before embarking on RCM, organizations often conduct an FMECA analysis to systematically identify and prioritize possible failures of a system, along with assessing their consequences and criticality levels.
Given that FMECA analysis yields valuable insights into the risks associated with system failures, it aids organizations in refining maintenance activities. By concentrating efforts on the most significant threats to system performance and reliability, FMECA assists in establishing appropriate maintenance tasks and frequencies.
FMECA and Reliability, Availability, Maintainability (RAM) Studies
The symbiotic relationship between FMECA and RAM is apparent in their complementary roles within engineering and system reliability. FMECA primarily aims at identifying potential failure modes, their effects, and their criticality, thereby offering valuable insights into the reliability aspects of a system. RAM analysis, on the contrary, concentrates on quantifying the reliability, availability, and maintainability of a system, typically through mathematical modeling and analysis.
FMECA findings can enrich RAM analysis by furnishing data on potential failure modes and their effects, enabling the estimation of the system's reliability and availability through the determination of failure rates and downtime. Conversely, RAM analysis can influence FMECA by pinpointing critical components or failure modes that exert a substantial influence on system reliability and availability, thereby guiding the focus of FMECA endeavors.