Reliability, Availability and Maintainability Study (RAMS Analysis)
- Marcio Pinheiro | Senior Consultant
- Oct 10, 2020
- 3 min read
Updated: Mar 14
In this article:
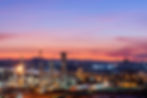
What is a RAM analysis?
Reliability, Availability, and Maintainability (RAM) are system design attributes that can have a substantial impact on the life cycle cost and performance of an engineered system. The purpose of RAM analysis is to ensure high production in maintaining high safety and quality levels for projects in any given industrial operation (oil and gas industry, offshore substation, carbon capture plant, hydrogen plant, etc.).
The objective of RAMS Analysis
At its core, RAM analysis entails representing a complex reality with a simplified model allowing for various types of analyses. Such a model can be used to predict performance, manage uncertainties, and reduce conservatism. Results from the analyses should be used to give sound and unbiased decision support, as well as identify bottlenecks and main contributors to reduced production and/or increased risk.
RAM analysis provides management decision support and input towards i.e.:
Predicted operational availability and project economics;
Equipment reliability including key production loss contributors;
Predictive maintenance strategy and spare parts philosophy;
Cost-benefit analysis towards alternative technical or operational solutions (sensitivity studies);
Main uncertainties related to production performance;
Identified possible causes for downtime;
Recommendations for improved production performance.
Methodology for RAM Study:
1. Establish a RAM study basis
Identification of key assumptions and associated degrees of uncertainty is considered vital to effectively produce as realistic and accurate results as possible, and for giving input to sensitivity analyses that might be necessary to cater to uncertainties. The key assumptions will be documented in the RAM analysis study basis. Assumptions are typically categorized into technical, operational, and analytical assumptions.
Close cooperation with different disciplines in the project is necessary to ensure an understanding of the process and operation that results in a robust and realistic basis for the RAM analysis. Because of this, it is proposed to arrange for a work meeting or similar with relevant disciplines when establishing the RAM analysis study basis.
2. Required Input
In order to perform the RAM analysis, a good understanding of the system to be analyzed is important for obtaining as accurate results as possible. Typical information required from the client to be used as input for the RAM analyses includes:
System description;
System schematics;
P&IDs;
Operational Philosophy;
Equipment capacity and redundancy;
Equipment failure data (if available);
Maintenance resources.
In addition to the above, one of the main premises for performing a successful RAMS analysis is the use of appropriate reliability data typically containing failure modes, failure rates and mean repair time. The application of data from literature and databases should always be thoroughly evaluated, to validate their relevance for the context in question. Reliability data sources include client experience data, OREDA, and the PDS handbook. ORS has access to a wide range of reliability data sources.

A Failure Mode, Effect, and Criticality Analysis (FMECA) if available is also a good input for the RAM analysis, especially for complex systems to give an accurate basis for system modeling.
3. Establish RAM model and run simulations
The RAM study basis and the reliability data are used to establish the RAM model, typically represented by reliability block diagrams (RBDs). The Monte Carlo method is normally used for the RAM model simulations to produce uncertainty ranges and confidence levels for the estimates. ORS uses the software Miriam RAM Studio for this purpose.
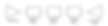
4. Analyse the results
The RAM analysis results from the simulation are analyzed and reported depending on the objective of the RAM study, for example, the expected availability of the system, the contribution for unavailability per equipment in the system, the impact of the maintenance program, and the lack of spare equipment in the plant availability.
The results are shaped in the best way to create value for the client by giving further information, for example, to decision gate process or for selecting the best cost-benefit solution and avoiding production losses.
Example of Results



ORS has supported a wide variety of clients within asset-intensive industries. ORS utilizes the advanced flow allocation software Miriam RAM Studio to produce a fit-for-purpose RAM model. Contact Per Ståle Larsen to discuss how RAM Studies can benefit your company.